Hi welcome to my 1964 VW Type 2 split screen campervan restoration blog. This will be a record of the vans restoration, and hopfully share infomation about bringing a splitty back to life.
Still on going
Machined front caliper mounts
Van Restoration Relocation
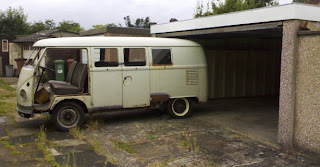
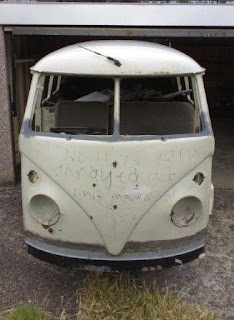
The vans trip to its new home went smooth, A few curtains twitch as a rusty heap was unloaded from the flat bed on to the street, Then, what I forgot to do was measure the width of the access lane to the garage. Pushing a van enthusiastically down an ally when you have 6in or less clearance either side and you don't have any breaks is a bit scary.
Having all this room In the garage didn't last long, to accompany the van came all the VW parts I’ve been hording for the last 10+ years (just in case I might just need that old rusty part), gear boxes, engines, tones of engine tin wear, exhausts, front beams and boxes of all the smaller bits. It's going to take some time to clear away the unwanted parts, and sort out a working garage, but in the end it should make getting the van back on the road so much more enjoyable.
Left "A" pillar and cab floor
Cab floor and door seal carrier repair
The bus also got it's first bit of sun for the summer.
Porsche brake conversion Pt3
Porsche brake conversion Pt2
Front Valance Pt3
I received the new lower front panel (which I specially requested without the cut out for the nose and longer at the ends so I can fold it over like the original.) Rather than butt weld this panel I joggled a small lip on the repair panel to sit inside the original one. I ground a ton of filler off the front panel so I could ensure the repair panel was straight, although a bit tricky around the nose; using some fabricating magnets and clamps the panel fitted OK.
Eager to get the panel on I started tacking it together, then double checking the fit before I went welding crazy I noticed that the joggle at the left corner end of the panel was overlapping to much, and causing the curve of the panels not to sit flush. Access to the back of this panel is very awkward because of the front light bowl and inner kick panel, this ruled out any fabrication from the back. So I painstakingly cut the joggle off from the front with a cut down junior hacksaw clamped in a pair of pliers. This did the job of letting the pannels sit flush, and then with the magnets in place I continued to tack it all together.
Learning from my cock up with warping the dog leg panel I spaced out the weld points and spot welded the a seam between the two panels with only a second spent on each weld, but still the original part of the panel had a slight ripple along its curve. Not sure if I’m being to particular about my work or still have a lot to learn but I'm determined to get it right. So I guess Ill rely on the paint prep to get rid of any imperfections (filler).
front door hindge replacement
Porsche brake conversion
porsche-brake-conversions technical info
After having a bit of a break from welding up the van, I spent a few late nights on the net working out the best option for the wheel and brake set up that I'd like. About 10 years ago I bought a set of 15"x6" Porsche Fusch alloys, I later found out from a friend that the guy I bought the wheels from had said they couldn’t be fitted to a van. Well, with that in mind, I saw it as a challenge.
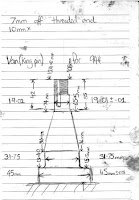
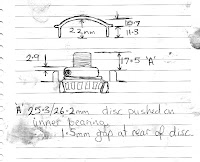
- Split 1964 king and link pin drums.
- Bay 1968 ball joint drums.
- Bay 1971-ish small stud Pattern discs brakes.